Pre-Stack Construction
Off-site Masonry
Atlanta, Georgia
Independent Research
Georgia Tech, Digital Fabrication Lab
Advisors: Russell Gentry, Jake Tompkins
Installation Team: Jake Tompkins, Michael Koliner
How will digital workflows rejuvenate traditional material application?
The masonry industry has been slow to adjust to the pace of BIM technology. Economic pressures indicate that not only does the role of the mason have to evolve, but the design methodologies and product delivery systems must be updated to leverage the inherent variability embedded in masonry systems.
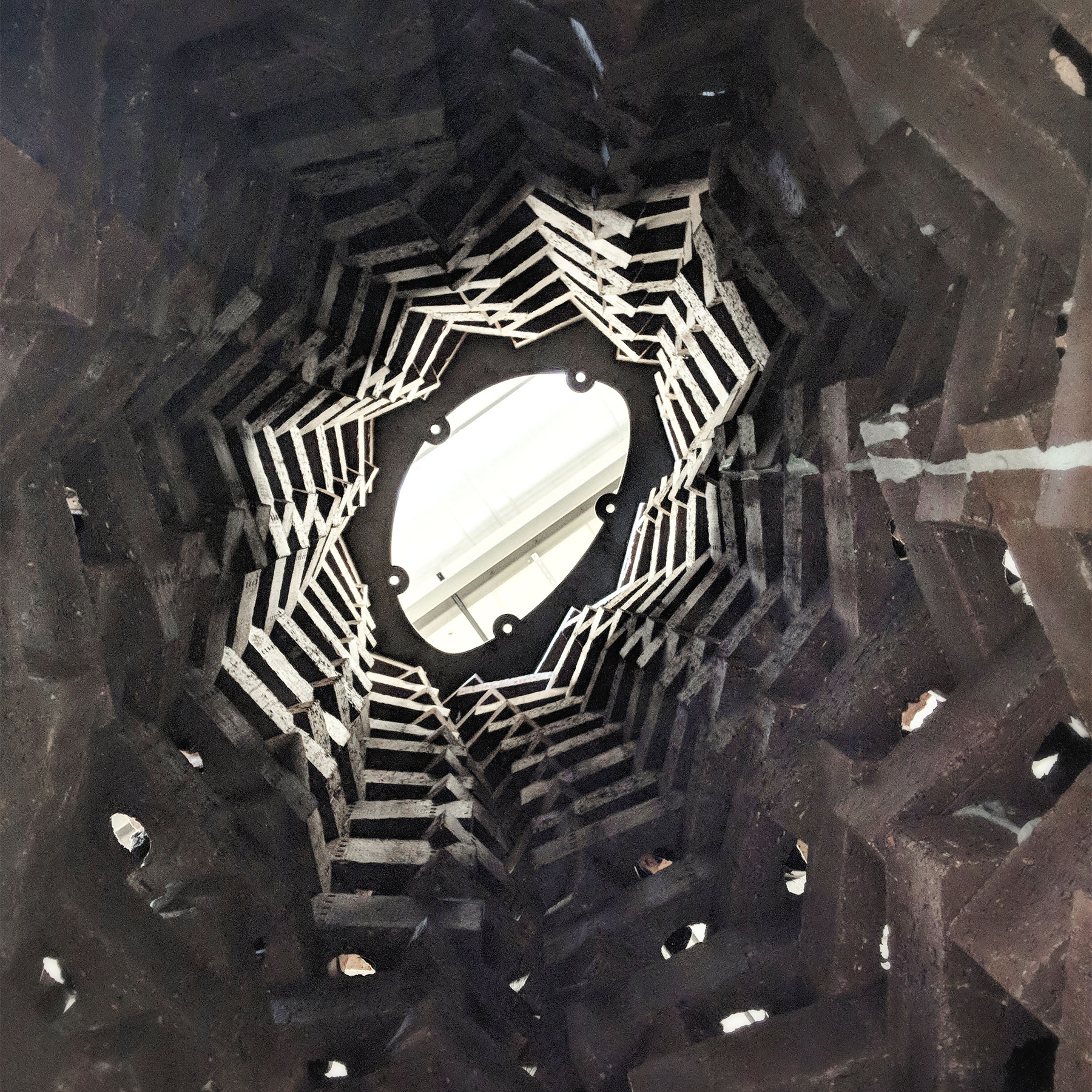
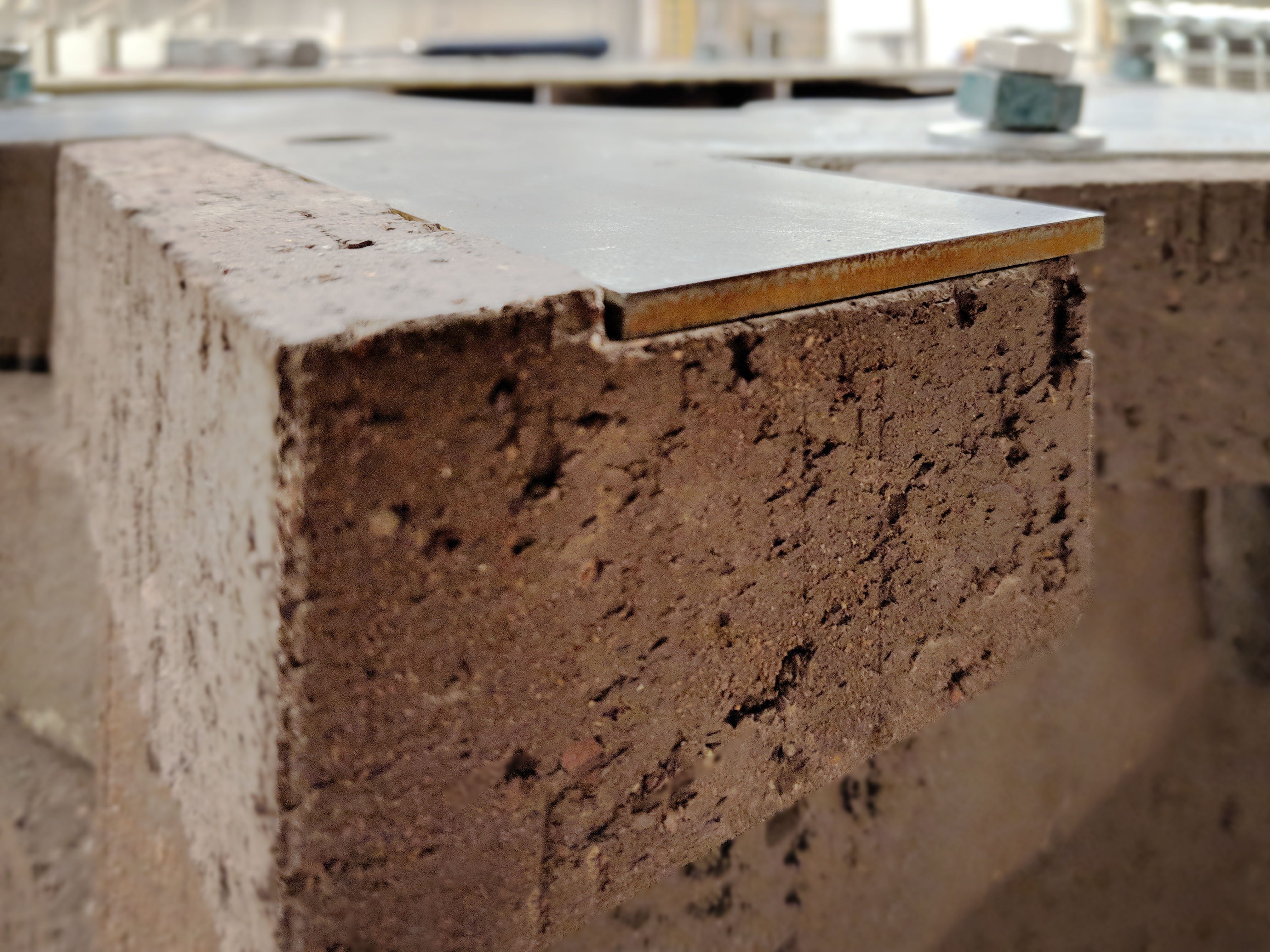
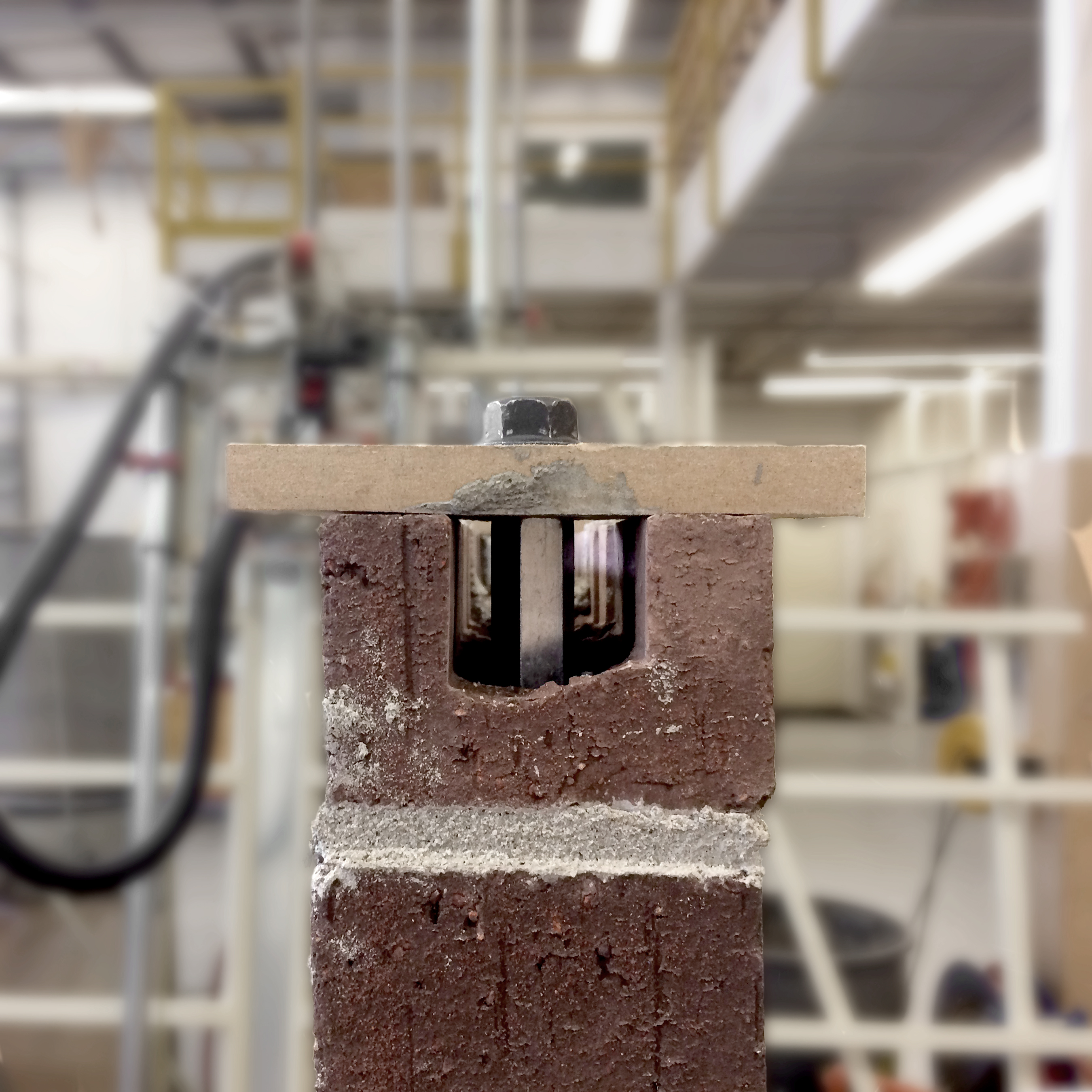
Customizing Masonry Units: Lap Brick with Flush Plate Steel, Channel Brick Customization of block types allows for compatibility with new reinforcement strategies and joinery.
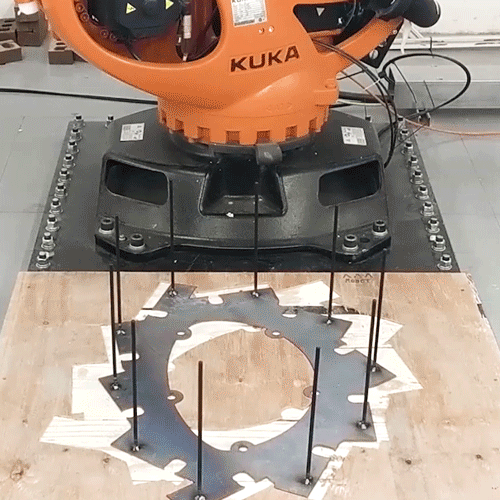
Robotic Stacking Process
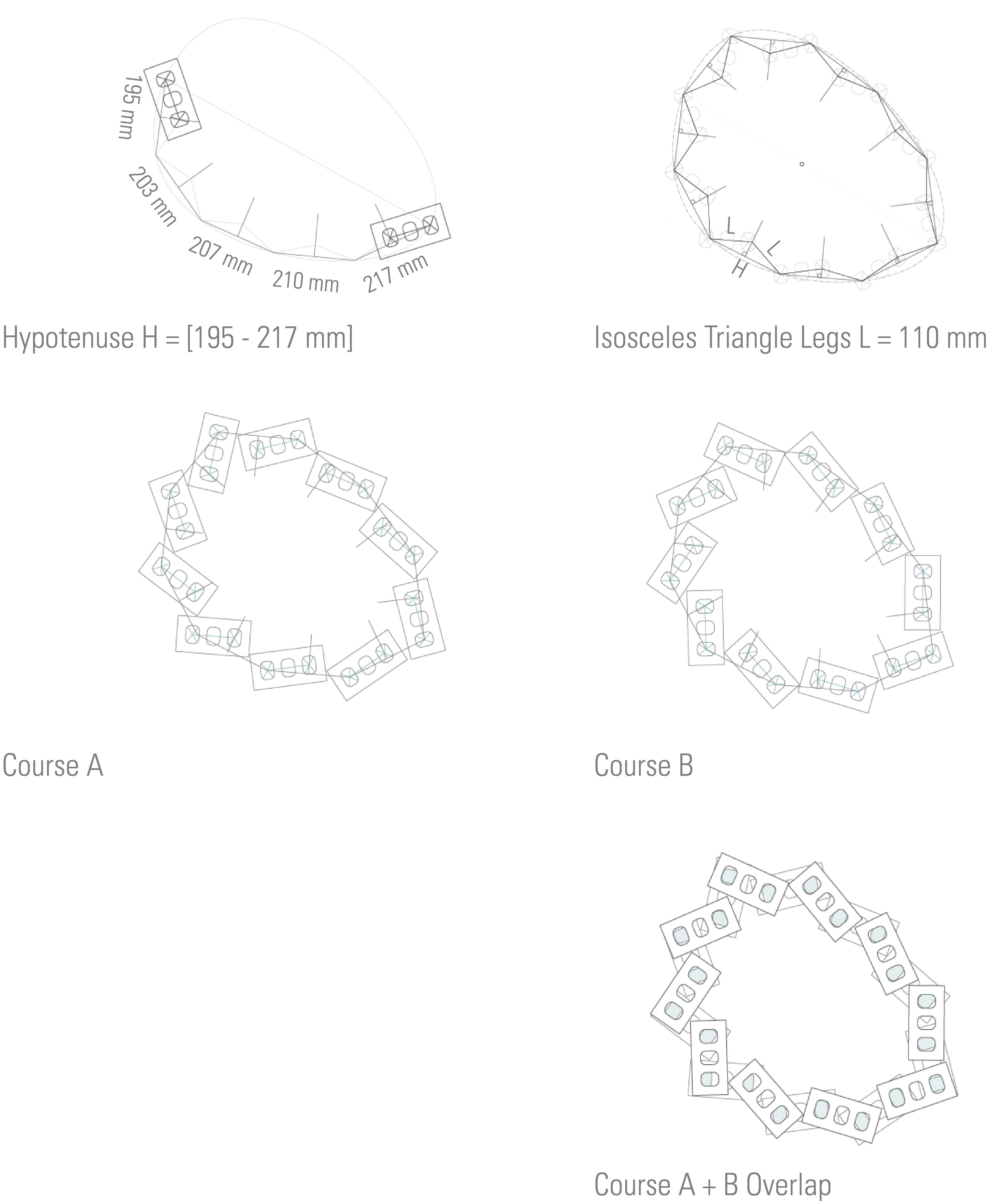

Core-fill Cross Sections
Structural integrity of the system relies on suitable fiber alignment in the grout. Cutting sections along a sample “grout channel” reveals the composition of the channel and provides feedback for refining mix design.

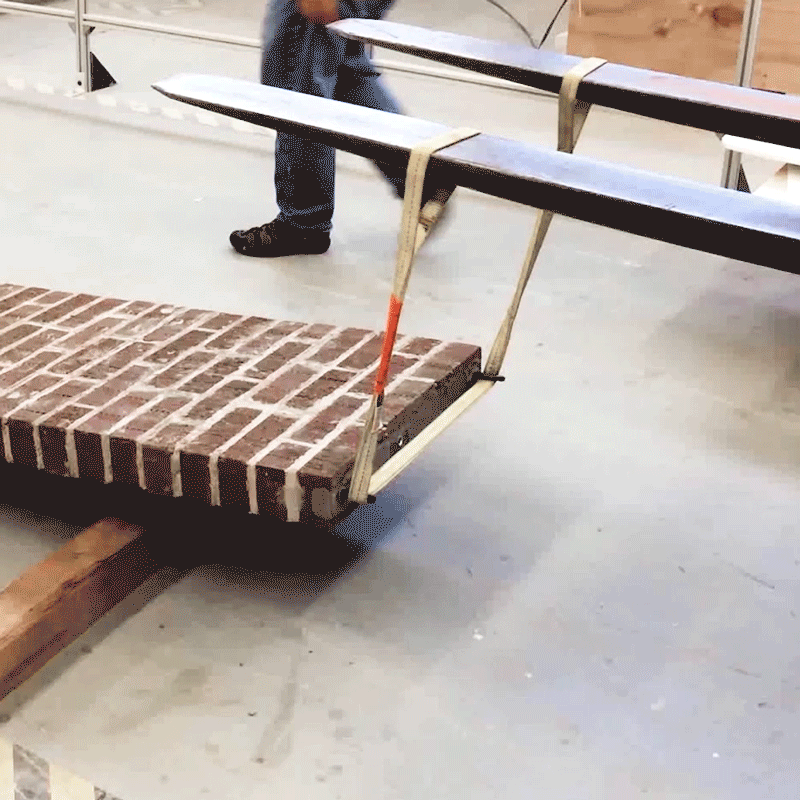
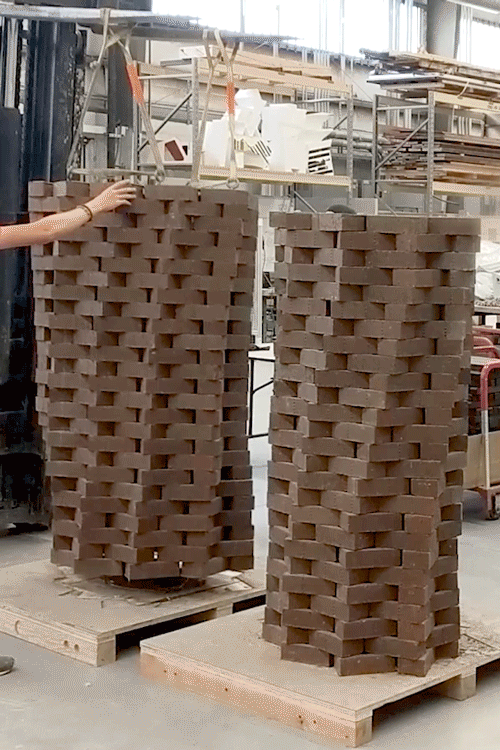
Structural Design Testing: Transportability
Reinforcement design was iterated to assess transportation viability. Suitable lateral reinforcement would allow structural units to be placed flat in truckbeds for transport, while lifting inserts would be necessary for installation on site.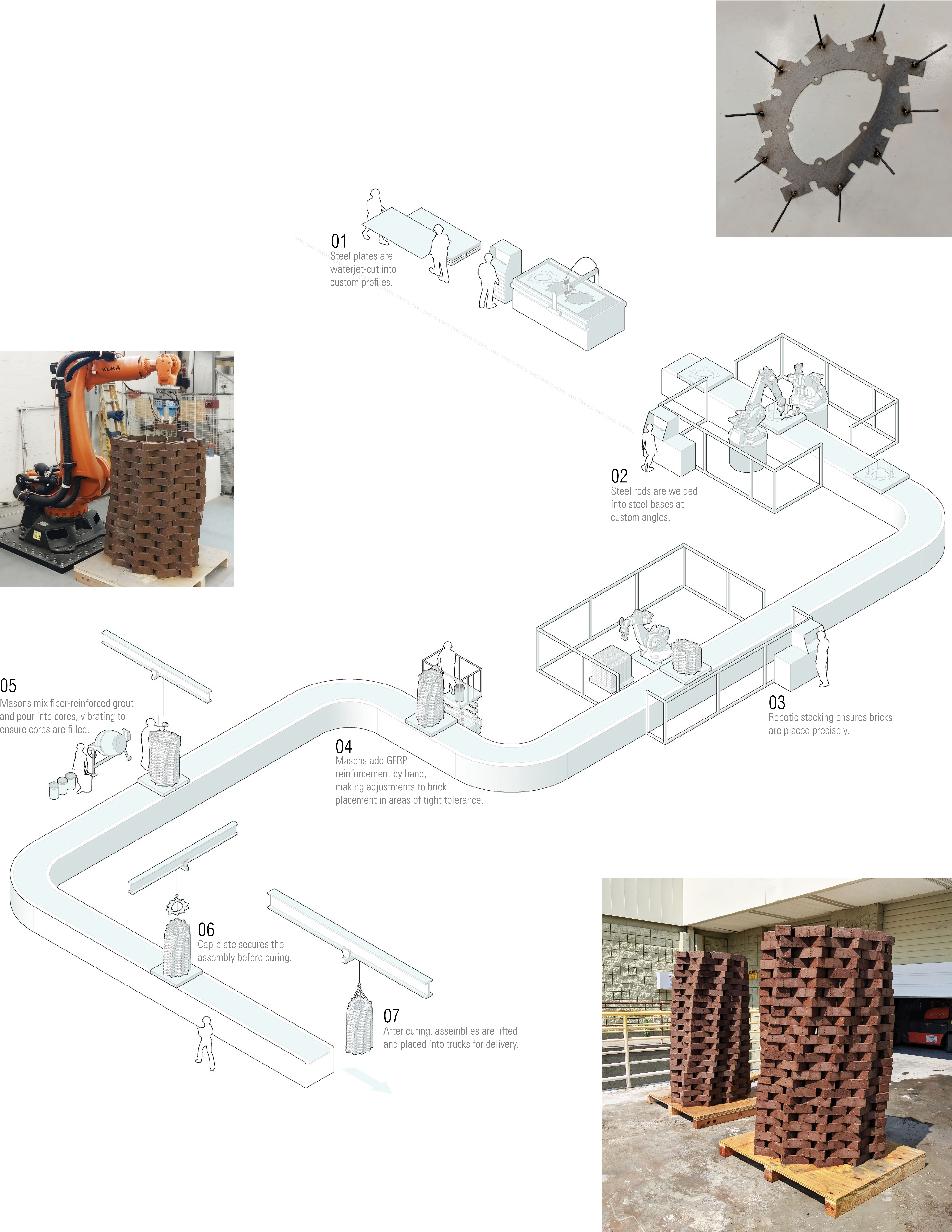
Merging Human and Industrial Productive Capacity
Stacking operations are repetitive and predictable, meaning that robotic arms can be suitably deployed. However, other parts of the process are highly variable due to the material quality of the blocks and environmental variation affecting the mortar or grout mixing process. Human masons can solve these variable issues faster than a robotic procedure can be developed, meaning that the manufacturing process benefits from the collaboration of humans and robots.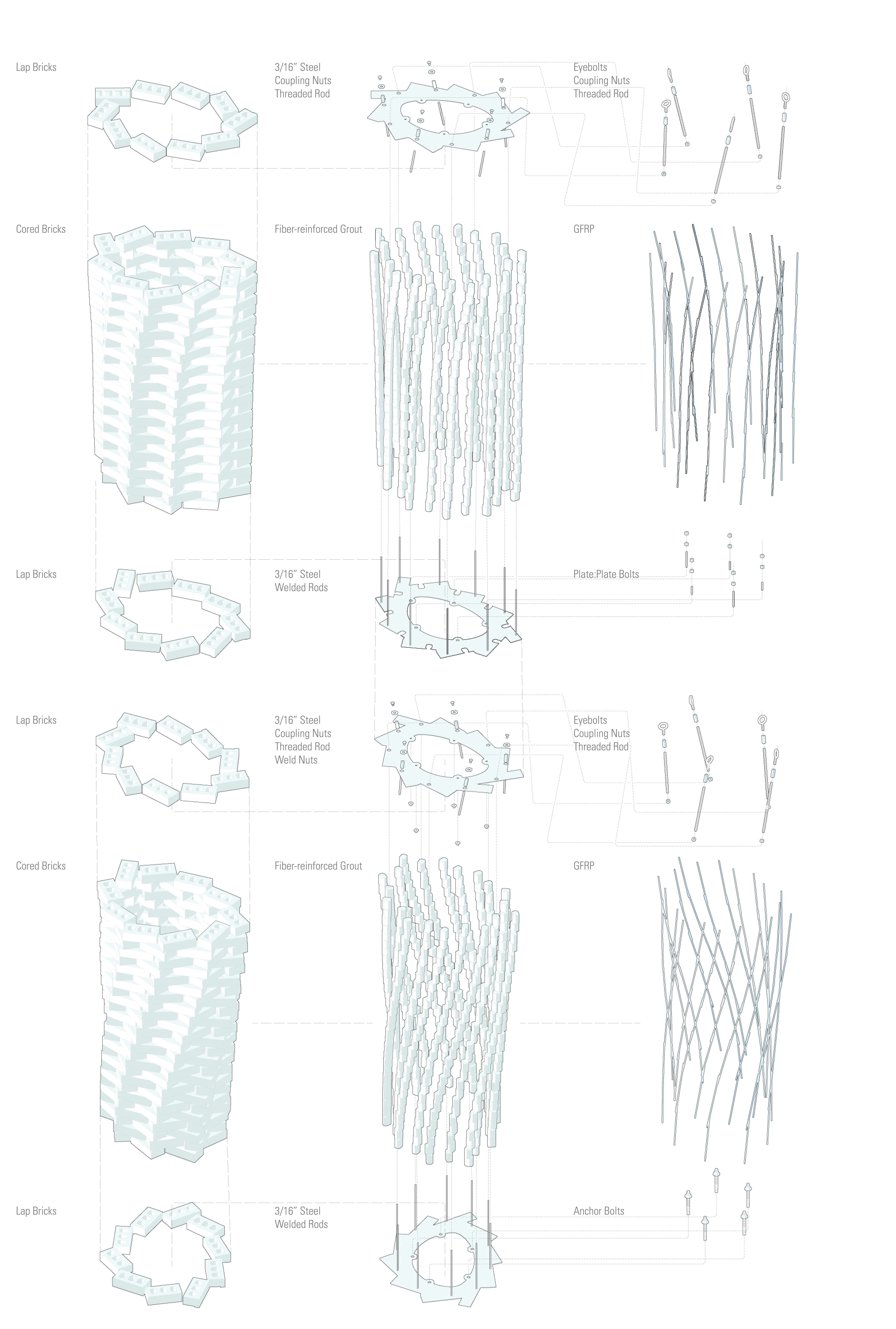
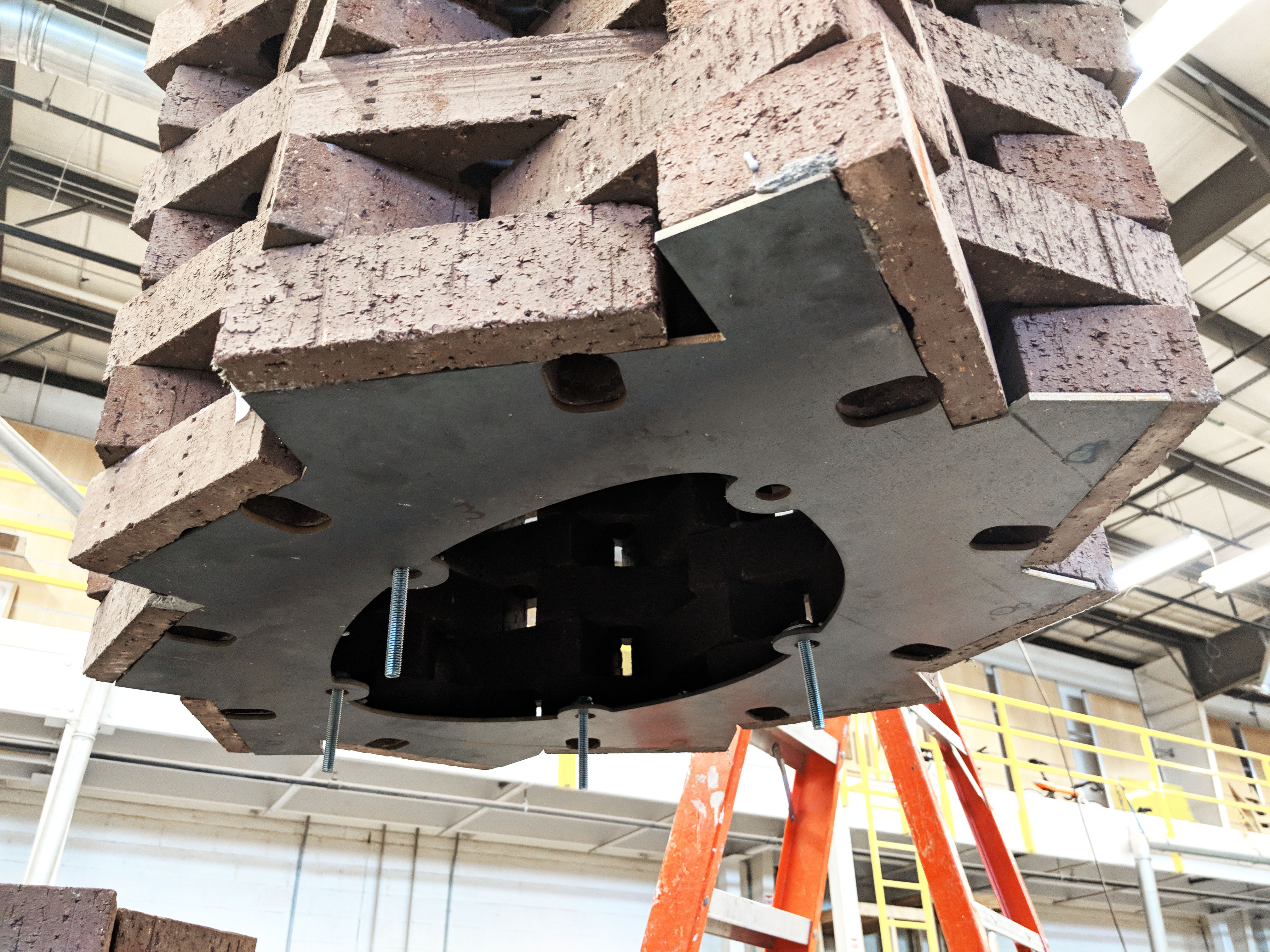
Baseplate Detail from Below
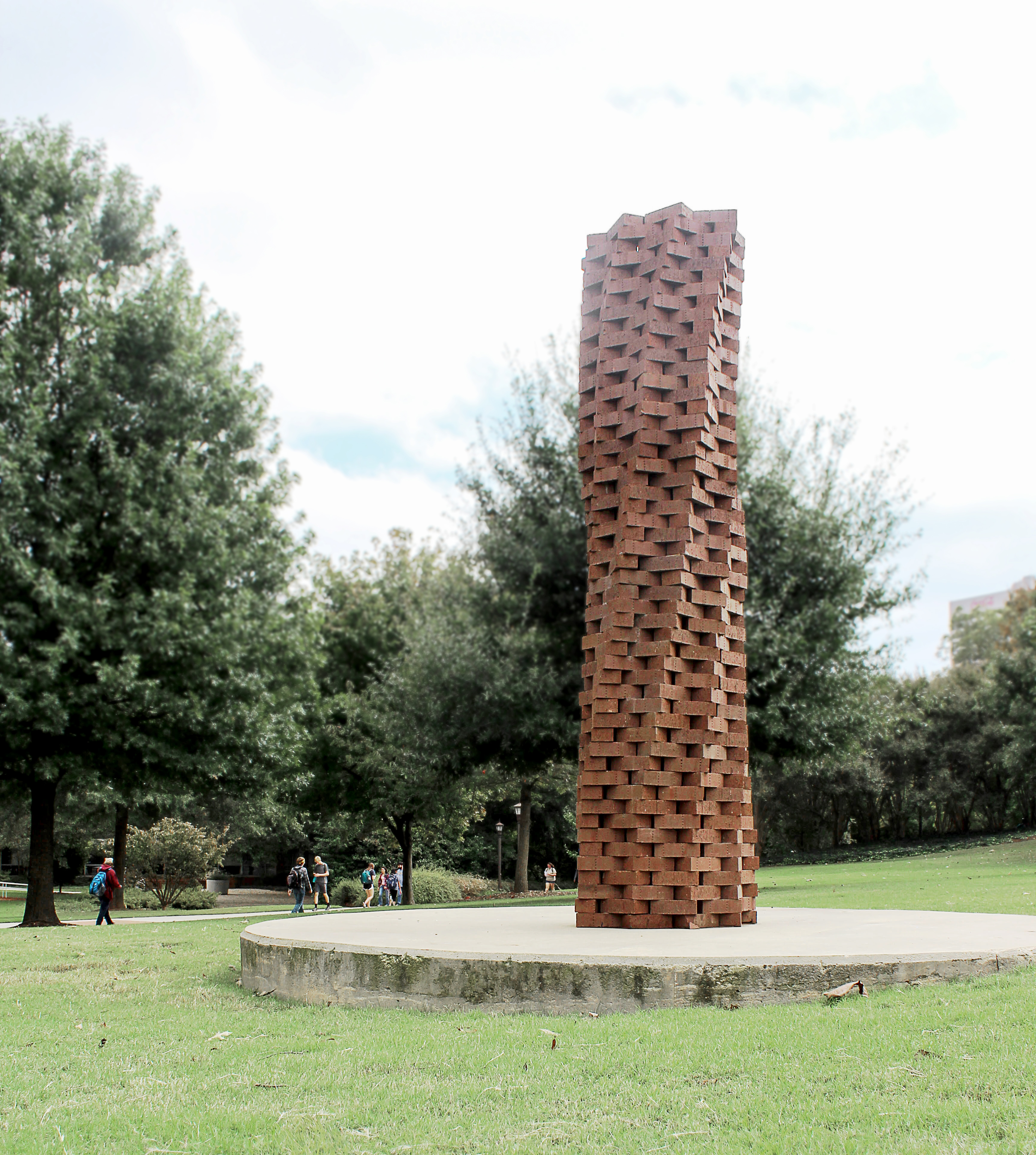
Installed Prototype